3D Reproduction Services
Quickly Replace Parts with Accuracy and Enhanced Features
When a machine or product relies on a specific part that is no longer available, damaged, or outdated, it can cause serious issues. Traditional replacement methods, such as CNC milling or casting new parts, are often expensive, time-consuming, and require large production batches.
With 3D printing reproduction, it is possible to replicate these parts quickly and cost-effectively, without high startup costs or long lead times. Thanks to modern manufacturing techniques, existing parts can be reproduced exactly, but also enhanced with stronger materials, more efficient designs, or additional functionality. This makes 3D reproduction an ideal solution for both industrial applications and consumer goods.
Which Parts Can Be Reproduced?
From Machine Parts to Technical Applications
The possibilities of 3D reproduction are virtually endless. Some common applications include:
Machine Parts – Gears, covers, clamps, sensor holders, and mechanical components.
Consumer Products – Casings, buttons, clips, or other small parts no longer in production.
Technical Applications – Custom holders, protective covers, or other functional components.
Automotive and Motorcycle Parts – Obsolete or worn-out components.
Architectural Elements – Replicas of ornaments or decorative parts.
Whether it’s a single part or a series of specialized components, 3D printing reproduction provides a fast, flexible, and cost-effective solution at your fingertips.
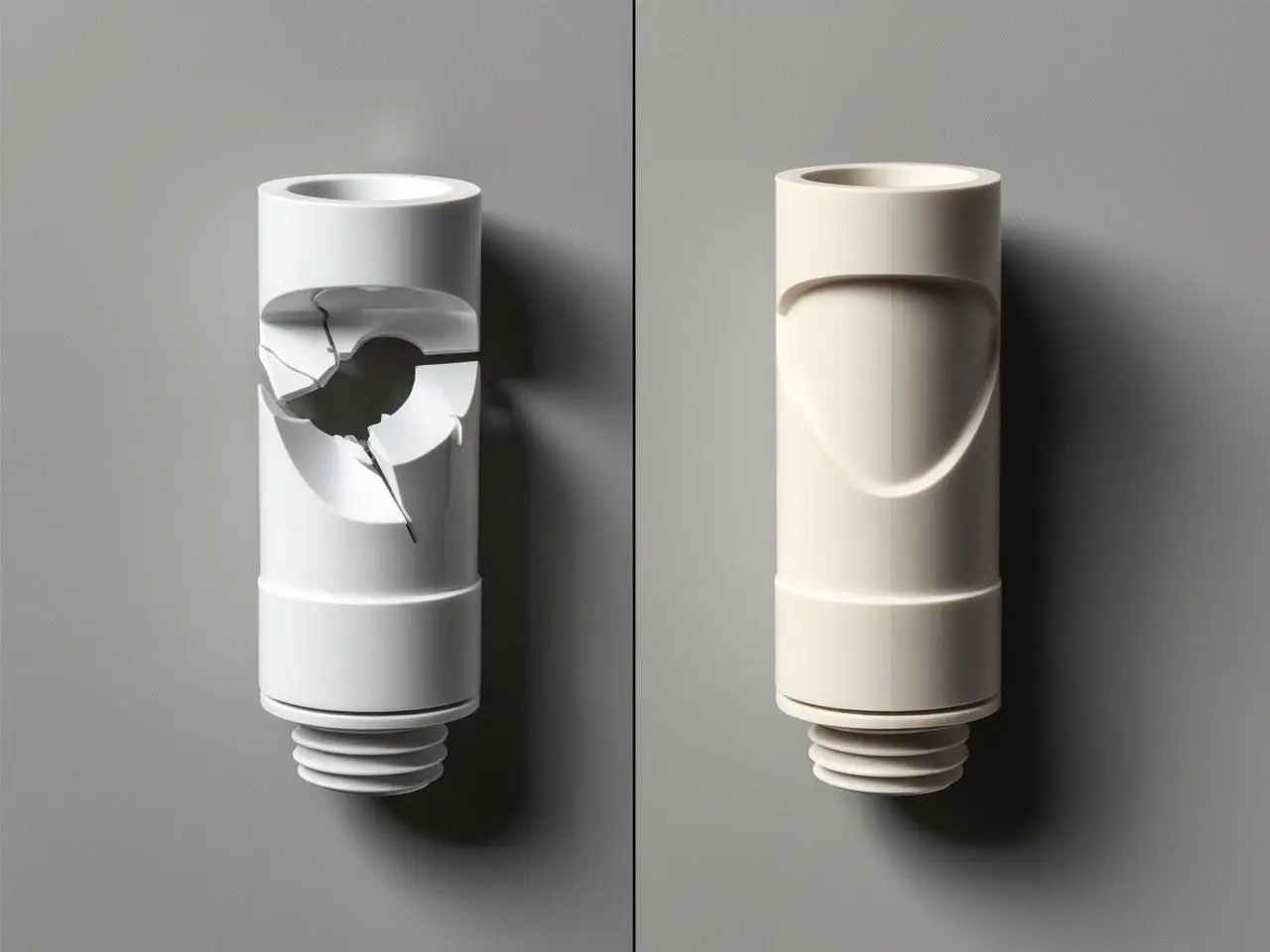
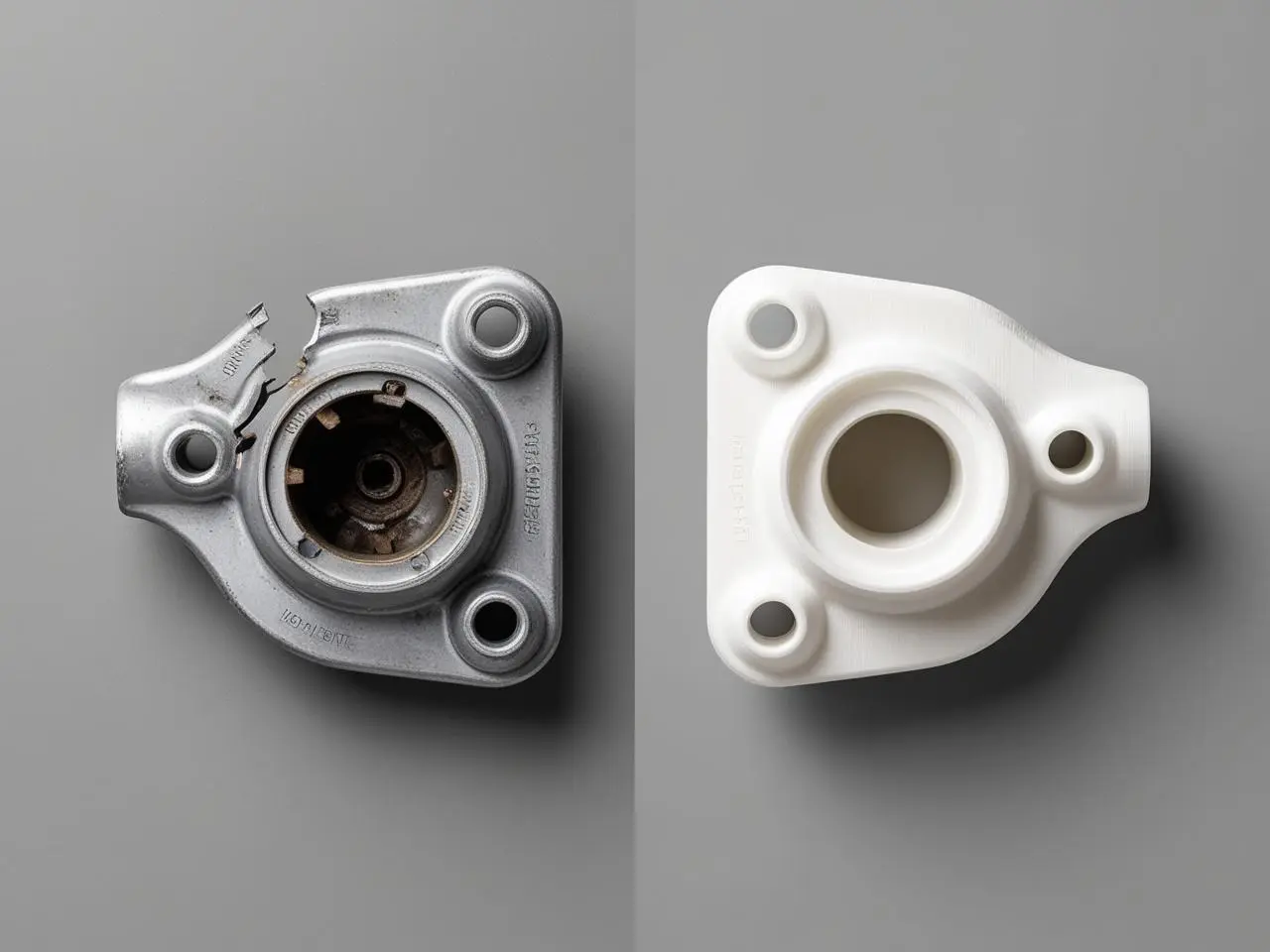
Why Choose 3D Reproduction
Optimize Time, Costs, and Quality for Your Parts
The advantages of 3D reproduction make it a smart choice for replacing parts:
Time and Cost Savings: No long lead times or expensive startup costs like casting or milling. 3D printing allows for the production of a single part or a small series without waste.
Precise Reproduction with a Perfect Fit: Parts are replicated or improved with high accuracy. Thanks to modern software and printing techniques, reproduced parts seamlessly integrate with existing components.
More Durable and Stronger Materials: Enhanced material choices make parts lighter, more wear-resistant, or better suited to heat and chemical exposure than the original.
Flexible Production of Unique Pieces or Small Batches: No minimum order requirements—whether it's a single spare part or a limited batch, without additional costs per piece.
Independence from External Suppliers: Parts that are no longer available or only sold in bulk can be reproduced directly and deployed without delays.
3D Reproduction Services Workflow
From Inventory to Delivery: Accurate and Efficient
The process of 3D reproduction of parts is a detailed and meticulous procedure, where accuracy, speed, and the right material properties are key.
Below is a comprehensive overview of the workflow for 3D reproduction, from the initial inventory check to the final delivery of the reproduced part.
The first step in the process is conducting a thorough inventory of the part that needs to be reproduced. This involves a detailed analysis of the following aspects:
- Function & Purpose of the Part: What is the function of the part within the larger assembly or machine? What role does it play within the product? Understanding the function is essential to select the right design and material.
- Technical Requirements & Accuracy: How precise does the reproduced part need to be? Should it be exactly the same as the original, or are some tolerance differences acceptable? What dimensions and specifications must be strictly followed?
- Material Selection: Which material is suitable for the part, considering the requirements for strength, flexibility, heat resistance, or other environmental factors? Does the part need to withstand certain chemicals, wear, or high temperatures?
Depending on the situation, an existing digital model is used (if available), or new models are developed. This may be based on sketches, technical drawings, reverse engineering of a physical part, or by measuring an existing component. The gathered data is then used to create a clear plan of action for the next stages of the process.
In this phase, the design is further optimized for production, with a special focus on improving the material properties and strength of the part. The goal is not just to replicate the part, but to improve it where possible:
- Strength & Durability: The original part may not always contain the best material for the specific application. In such cases, a different material may be chosen that is stronger or more durable, such as a more wear-resistant plastic or composite. This can lead to a longer lifespan of the part in its application.
- Lightweight & Flexibility: For some parts, it may be beneficial to choose a lighter material, especially for parts that need to move quickly or those that should not add too much mass to the product.
- Improvement of Weak Points: If there are weak points in the design of the original part, these can be addressed. This could involve redesigning certain geometries or reinforcing parts that may otherwise wear out or break quickly.
Based on the requirements and preferences, the most suitable material is chosen, considering the properties of various materials (such as thermoplastics, metal composites, elastomers, etc.). Together with the selection of the appropriate manufacturing process, this ensures an efficient and reliable reproduction.
After the design and material selection are approved, the process moves to the actual production of the part. We utilize advanced 3D printing technologies that offer the highest precision and efficiency:
- SLA (Stereolithography): This technology is ideal for creating highly detailed and accurate parts, often used for small series or prototypes where high detail accuracy is required.
- SLS (Selective Laser Sintering): This technique uses a laser to melt and fuse powder layers. SLS is ideal for functional parts that need to be stronger and for a wider variety of materials such as nylon, fiberglass, or metals.
- FDM (Fused Deposition Modeling): This technique is often cost-effective for larger parts or series and is ideal for making parts from durable thermoplastics. FDM is a versatile technique and can print many different types of plastics depending on the strength and flexibility needed.
Depending on the type of part and the required properties, the appropriate printing technique is chosen. The 3D printing process is carefully monitored to ensure excellent precision and reliability. In some cases, multiple printing techniques are combined to achieve the optimal result.
After printing, the part may not be immediately ready for use. Depending on the specifications and the desired final result, various post-processing steps may be required to refine the part:
- Sanding & Finishing: The surface may be sanded to remove any imperfections or edges, ensuring the part looks visually perfect and fits well with other components.
- Coatings & Painting: Some parts need an additional protective layer to guard against chemical influences, wear, or other environmental factors. Coatings or paints can also be applied for aesthetic purposes.
- Assembly: If the part consists of multiple components, it will be assembled to create the final product.
Each reproduced part is then strictly inspected to ensure the desired quality. This includes testing the accuracy of the design, the strength and functionality of the material, and the fit of the part. The components are tested according to predefined specifications and quality standards to ensure they meet the customer's requirements.
One of the major advantages of 3D reproduction is the speed of production. Thanks to advanced 3D printing techniques and efficient workflows, parts can be produced and delivered quickly. This minimizes downtime and production loss.
- Quick Response Times: Since the 3D printing process is relatively fast compared to traditional manufacturing methods, parts can be produced and delivered in a short time, even for rare or hard-to-find components.
- Flexibility in Quantities: Whether it's a single replacement component or a limited run, 3D reproduction offers the flexibility to produce parts in the required quantities without unnecessary costs.
- Cost Savings: The fast production and elimination of startup costs for traditional methods like casting or milling result in significant cost savings. This is especially beneficial for small batches or when a quick replacement part is needed.
With our advanced processes, we can respond quickly and ensure the efficient delivery of reproduced parts, so your production doesn't come to a halt and operational continuity is maintained.
By combining advanced technology, material expertise, and a precise methodology, we deliver reliable and custom parts with the highest quality standards.
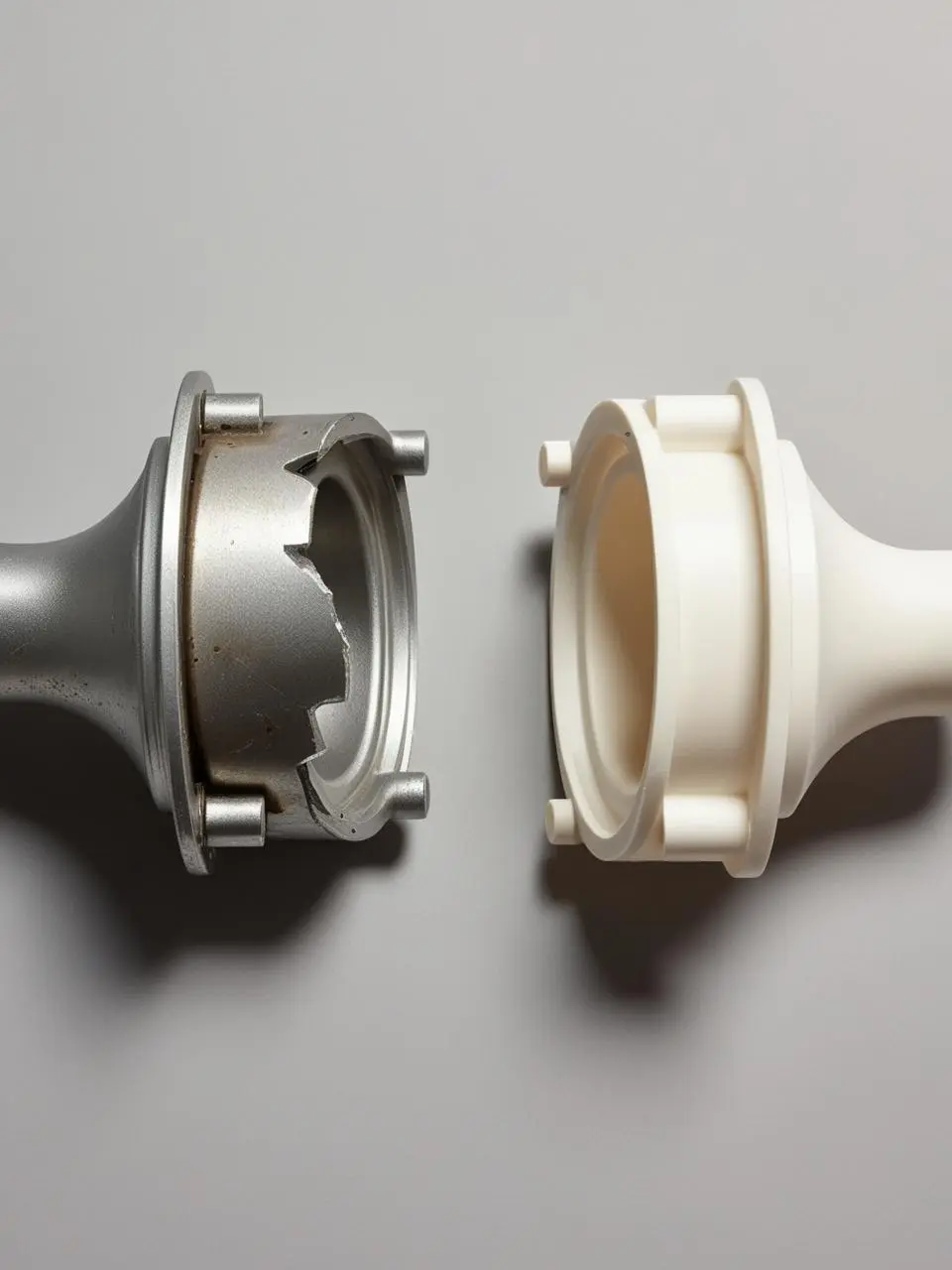
3D Reproduction Request Form
Fast and Precise Reproduction – Get a perfect replacement without long lead times.
Cost-Effective & Flexible – Single pieces or small batches without high startup costs.
Stronger & More Durable Materials – Enhanced parts with optimal performance.
ContactNeed a Replacement Part Fast?
Accurate and Cost-Effective, Without Long Wait Times
Is a crucial part worn out, damaged, or no longer available? With 3D reproduction, an accurate replacement can be created quickly, without high costs or long lead times.
Upload your model or contact us directly to discuss the possibilities. A custom solution is faster and more accessible than ever.